Comprehending Just How a Chemical Defoamer Functions to Improve Industrial Processes
Chemical defoamers play a crucial duty in maximizing industrial processes by efficiently reducing foam-related challenges. What remains to be discovered is just how these defoamers can be tailored to meet specific functional needs.
What Is a Chemical Defoamer?
A chemical defoamer is a compound specifically formulated to reduce or remove the development of foam in various industrial processes. Foaming can disrupt manufacturing efficiency, influencing the high quality and performance of items in markets such as food and beverage, drugs, and wastewater treatment. Defoamers are vital in these applications, as too much foam can bring about functional obstacles, such as overflow, lowered mixing effectiveness, and hindered warmth transfer.
The option of a proper defoamer is important, as various solutions may be customized for specific processes or kinds of foam. Variables such as compatibility with other components, temperature level stability, and the designated application play a substantial role in the efficiency of a defoamer.
Devices of Defoaming Action
The systems of defoaming activity entail intricate communications in between the defoamer and the foam structure. When a defoamer is presented to a foaming system, it migrates swiftly to the surface of the foam bubbles, displacing the maintaining agents that contribute to foam stability.
As smaller bubbles merge into bigger ones, the overall security of the foam diminishes. In addition, particular defoamers might contain hydrophobic components that enhance their ability to destabilize the foam by developing an obstacle that hinders bubble formation. This double activity-- surface area stress decrease and destabilization-- permits for an extra reliable failure of foam.
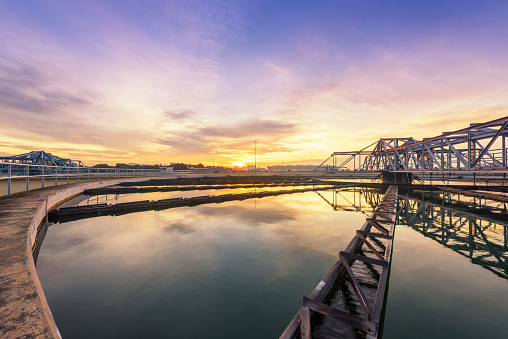
In addition, the thickness and dispersing attributes of the defoamer play important roles in its effectiveness. A well-formulated defoamer will guarantee fast movement and optimum efficiency, minimizing foam development during commercial processes. By understanding these mechanisms, sectors can much better select and apply chemical defoamers to improve functional performance and item quality.
Sorts Of Chemical Defoamers
Chemical defoamers can be categorized into several types, each tailored to certain applications and foam difficulties. The main classifications consist of silicone-based, non-silicone-based, and powder defoamers.
Silicone-based defoamers are highly efficient because of their ability to spread out quickly throughout liquid surface areas. They offer outstanding foam reductions and security, making them ideal for various industrial applications, including coverings and adhesives. Non-silicone-based defoamers, on the various other hand, frequently count on organic compounds like fatty acids or esters. These are particularly preferred in food and beverage markets as a result of their low toxicity and governing compliance.
Powder defoamers contain strong bits that can be added to completely dry procedures or formulations. They are frequently used in procedures where fluid defoamers might not work, giving a special service for specific applications, such as in the manufacturing of certain types of plastics or powders.
Additionally, each type of defoamer can be customized with different ingredients to boost performance, such as surfactants or emulsifiers, allowing for convenience in dealing with different lathering scenarios across numerous sectors.
Applications in Industrial Processes
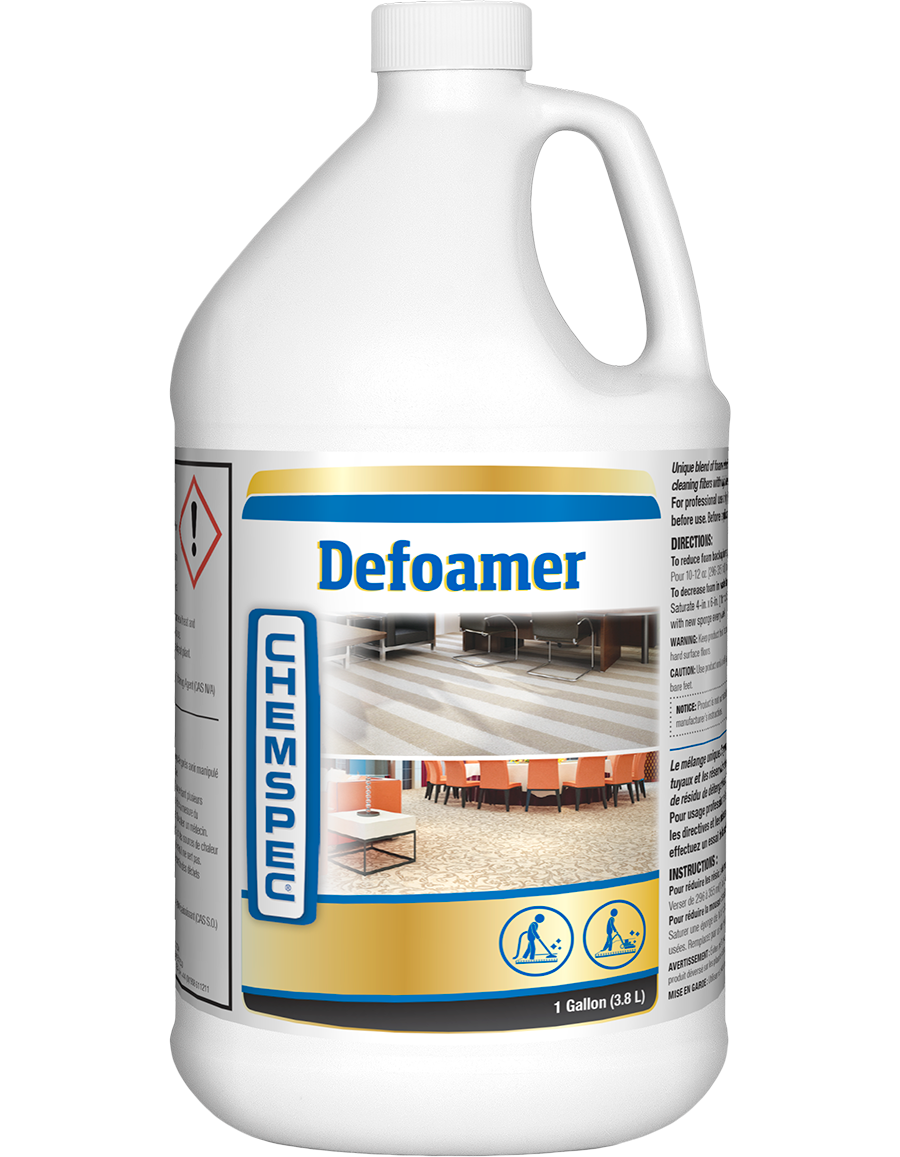
In the food and drink sector, defoamers are critical during the manufacturing of juices, beers, and milk items, where too much foam can impede blending and purification procedures. By lowering foam Bonuses formation, defoamers help keep regular product top quality and maximize processing times.
In pharmaceuticals, the visibility of foam during the mixing and formula of medicines can influence dosage accuracy and product security. read here Defoamers make certain smooth operations, therefore promoting the manufacturing of high-grade drugs.
Wastewater therapy centers additionally depend on defoamers to regulate foaming in oygenation storage tanks, which can or else lower treatment effectiveness and complicate sludge handling. By effectively taking care of foam, these chemicals enhance the general efficiency of treatment processes and add to regulatory compliance.

Advantages of Utilizing Defoamers
While foam can provide substantial difficulties throughout numerous markets, the usage of defoamers supplies countless advantages that enhance operational efficiency and product stability. Defoamers properly remove or decrease foam formation, resulting in smoother production procedures and improved product quality. This decrease in foam reduces disturbances throughout production, permitting continuous operation and increased throughput.
Furthermore, the application of defoamers can bring about set you back financial savings by reducing the need for excess resources and energy intake related to foam administration. By maximizing the production procedure, makers can attain greater yields and reduced waste, eventually improving success.
In addition, defoamers add to better devices efficiency. Foam buildup can bring about clogging, overflow, and tools wear, causing pricey downtime and maintenance. By preventing these issues, defoamers prolong the life expectancy of equipment and lower functional costs.
Final Thought
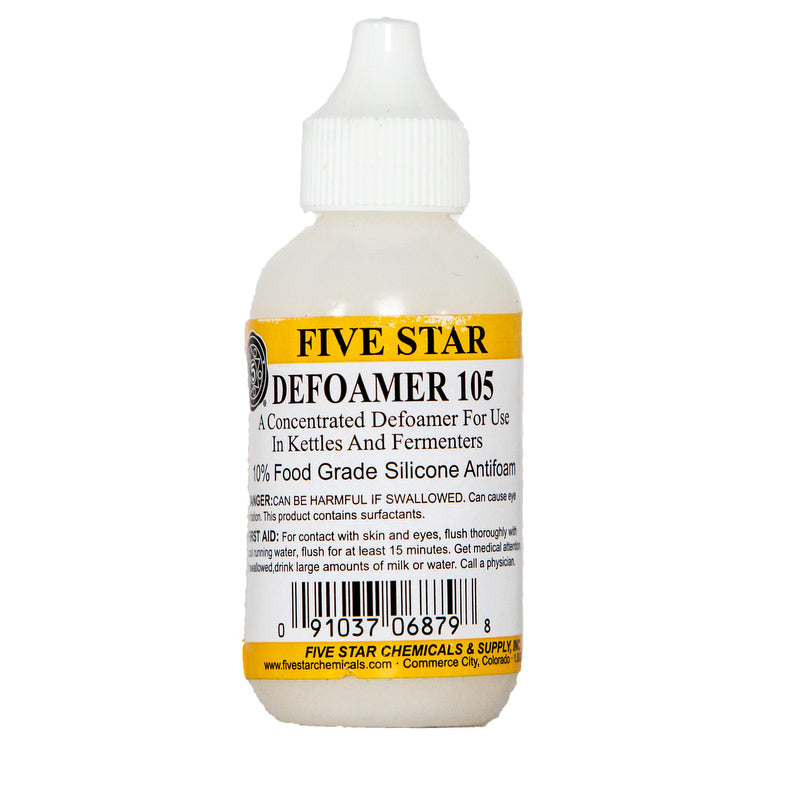
A chemical defoamer is a material particularly formulated to remove the development or minimize of foam in various industrial processes. When a defoamer is introduced to a lathering system, it moves quickly to the surface area of the foam bubbles, displacing the maintaining agents that add to foam stability. A well-formulated defoamer will make certain rapid movement and optimum performance, minimizing foam development throughout industrial processes. Defoamers effectively eliminate or decrease foam development, leading to smoother manufacturing processes and enhanced item quality.In final thought, chemical defoamers play an important duty in boosting commercial processes by effectively lowering foam Resources formation.